Jenny Smith Andrews at H+H, offers her views on why the Fabric First approach is the best foundation for building to the regs and higher.
Using the correct methods, we believe it is more than possible to build cost effectively to planning and building regs requirements with minimal or even no use of renewable technologies.
We also believe that this can be done without entirely rethinking the way houses are designed and built. Only small tweaks are required in fact, not the radical departures that some advocate.
Why a Fabric First Approach Makes Sense
Putting as much effort as possible into the fabric of a home makes sense in many ways. In contrast to renewable technologies, a building’s fabric can’t be meddled with by tenants, in any significant way. Built correctly it will continue to perform as intended for decades and easily have other technologies added in future if required.
Compare that with how complicated some renewable technologies are, especially their control interfaces. Most people can work a simple thermostat dial but give them a complicated control, of which there are many, for any ground or air source heat pump, micro CHP or biomass boiler and it’s a different ball game.
It means either you have to spend time and money, as some local authorities have done, educating and training tenants how to use the equipment. Or, tenants use the technology incorrectly, turn it off, or worse, resulting in a home running in anything but an energy efficient capacity.
Such technologies also advance at frightening pace. In ten years what’s to say that technology installed now will not be inefficient and need upgrading? All this adds long term costs that can be unforeseen when costs to build an airtight and thermally efficient building envelope can be factored in from day one.
Case Studies of Fabric First Builds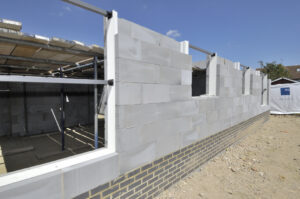
Ashford Council is just one example of a local authority building this way. They had a clear objective to build high quality houses that will last for decades, being able to withstand the rigors of a number of different tenant families over time. The homes also had to be easy and comfortable to live in, delivering excellent U-values and air-tightness in the process.
The chosen solution was the H+H Rå Build method of construction. This uses the H+H Thin Joint
masonry system with either solid wall or fully filled cavity walls using aircrete blockwork.
Airtightness is perhaps the most challenging aspect of building to high fabric standards. However, it was the substantial benefit in reducing heat loss that was the single most significant factor in the decision to use Rå Build.
In designing the wall structure, the use of aircrete’s very low psi values, based on Accredited Construction Details, allowed a halving of the y-value from 0.08 to 0.04W/m2K.
This is used to calculate the impact of linear thermal bridging within SAP. The 0.04 y-value is achieved by virtue of the thermal efficiency of aircrete and has a similar effect on all external elements.
For the Ashford development cavity external walls were used with high performance full-fill cavity wall insulation manufactured by Superglass was used in the 125mm cavity. The structural width of the whole cavity wall was no more than 325mm with a U-value of 0.19W/m2K using two Thin Jointed leaves of 2.6N/mm2 aircrete. However, taking into account the 0.04 reduction in the y-value meant that the walls effectively provided a U-value of 0.15W/m2K.
To complete the energy efficiency of the build, solar PV panels were used on the roof of the dwellings. It was necessary to include some renewables in this project to achieve Level 4, but the contractors did note that the very thermally efficient structure significantly reduced the PV requirement.
Renewables are not the only answer to building to higher levels of the performance. H+H is involved with an initiative to understand how houses can be built to high levels or performance without using any sources of renewable energy.
AIMC4 is funded by the Technology Strategy Board and represents a unique collaboration between housebuilders, designers and product manufacturers to produce standard house designs that meet the demands above and beyond the building regulations purely through the efficiency of the fabric of the building. This must be the most sustainable answer providing structures that are inherently efficient throughout the lifetime of the building.
Our involvement with these pioneering projects demonstrates that aircrete, building on familiar design formats and UK site practice, represents a future proofed building fabric solution.